
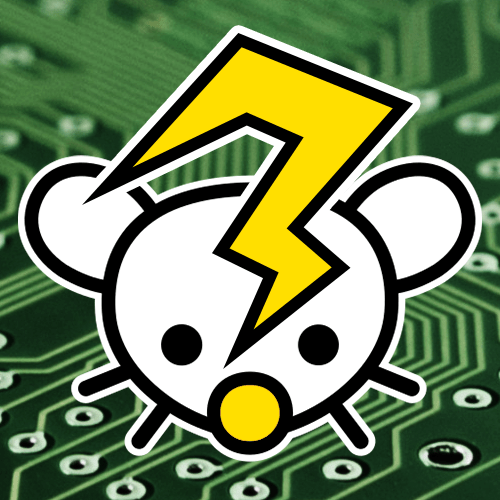
I believe this lead configuration was designed to help with vibration resistance at very low cost, negating the need for a glue down. It could also be a bit more compatible with conformal coating? I suspect they’re special order on account of the leads and maybe the dimensions (could be demanding at the time), and the space constraints didn’t really allow them to claim a full 680μF.
I’ve never tried super hard, but I’ve never manged to source these from anywhere. I think this technique has mostly been replaced by multi-lead (three to five) configurations. I don’t think I’ve seen these from anything built in the last 20 years or so. I suspect you’ll have to retrofit to get things running again.
There’s some risk but I’ve managed to make a standard snap-in capacitor work by using a pair of pliers to rotate one of the leads on it’s rivet and bending both leads for the proper angle. This doesn’t help with vibration so I’d recommend fixing it with selastic as well.
Alternately you can modify the board to fit standard capacitor leads if everything lines up ok. Don’t forget that the PTH in the mounting holes might be connecting planes on opposite sides of the board. Make some sturdy vias if necessary.
If you’re really feeling froggy you can take a page from the vintage electronic restoration handbook and (kind of) restuff the cap. It’s usually done to be pretty, but in this case you could do it without care for looks and only in order to retain the terminals. This may be unwieldy given the size. I imagine it’d essentially be cutting the base off, wiring it to the new cap, and gooping everything together neatly with silicone.
Hasn’t come up yet in a handful of tries over the years. The clamping force in the ones I was working with was insufficient to turn the rivet when the lead was rotated so I don’t suspect damage. The potted/sealed caps wouldn’t tolerate this at all, nor would any given particularly well riveted model. I totally understand not wanting to get weird with expensive parts. The one’s I was working with were only a few USD.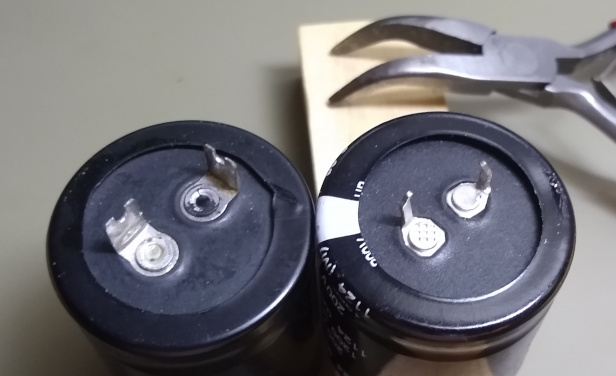
I figured I’d dig through the junk pile and see if I could demonstrate. On the left is an Elna CE-W series 470μF 200WV, Ø30mmx50mm I had lying around, probably from the late 80s/early 90s. These are likely from an old switching supply, back when they made them specifically for US 120V mains. Just included it for fun as I wasn’t sure I still had one around.
The one on the right is an unbranded 1200μF 200WV Ø30mmDx35mm with a 2011 datecode. I used the pliers in the background to give one of the leads a 90deg turn. It’s dodgy with such thin leads as these, but it can be done. Solder tie lugs are much better as they have a flat square lead shape that’s less likely to tear off. So definitely possible, but definitely dodgy.
I don’t always have the best ideas, but I do tend to have a lot of them. :)
I try to cast a wide net cause it’s not always obvious what priorities folks have in their repairs. I doubt anyone would care about the aesthetics, for sure, but you would get to do all your arts and crafts work without involving the board itself, which could make some folks nervous.
If you have time for the shipping you can get some Kafuter K-704N from aliexpress et. al. pretty cheap. It’s exactly the white selastic used for electronic holddown. Also the datasheet for whichever capacitor you order should have details for the recommended board footprint and drill size so you can be sure things will line up.
Glad to help :)